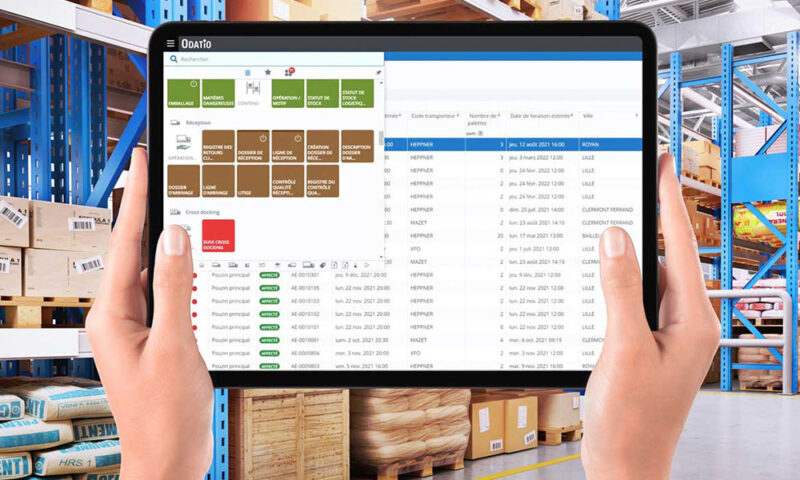
Creating a seamless ecosystem that connects everything in the logistics continuum
Currently, the logistics and supply chain industry, especially in the MENA region, is being transformed by a diverse array of innovative technologies. It is hard to pinpoint a single technology as a primary catalyst, as it is the entire ecosystem or the interplay of various technologies driving this change. From software solutions to advanced robotic fulfillment systems, including Autonomous Case-handling Robots (ACR) and Autonomous Mobile Robots (AMR), the key innovation lies in how these elements are seamlessly integrated.
The real game-changer is how software and automation work together. It is not just about having cutting-edge robotics in your warehouse; it’s about creating a seamless ecosystem that connects everything from software orchestrating operations within the warehouse to ERP systems, last-mile delivery, and passport management systems. This holistic and integrated approach is revolutionising the industry, driving innovation and efficiency.
At the end of the day, it is all about creating a unified, end-to-end solution that enhances efficiency and ensures all the different pieces of the supply chain work together seamlessly. This is what sets companies apart in the MENA region, making logistics operations faster, more accurate, and more competitive.
LogisticsGulf.com interviewed Alain Kaddoum, Managing Director, Savoye Middle East.
LogisticsGulf.com (LG): How are automation and robotics shaping the future of warehouse management and distribution centres, and what key benefits are these technologies bringing?
Alain Kaddoum (AK): Building on the previous discussion about robotics and automation in warehouses, these technologies offer significant added value beyond their traditional benefits of saving space, increasing accuracy, and speeding up operations. At present, automation and robotics are revolutionising the industry through their adaptability and ability to integrate seamlessly with other systems.
The key focus is on the agility and modularity of solutions and adopting technologies that can adapt, grow, and even be customised over time. For instance, modern systems can allow flexibility in storage size without the need to change the robot itself. This agility is crucial for businesses that require their warehouse systems to evolve as their needs change.
Another major area of innovation is AI integration into robotics. In the current systems, robots operate in a reactive mode, repeating pre-programmed actions with precision. However, the future of warehouse management involves smart warehouses where AI enables robots to make decisions autonomously.
For example, instead of pre-teaching a robot on how to pick up an item, future robots will use image processing algorithms to identify objects – whether it is a bag, bottle, or item with a complex shape – and decide in real-time how to pick them.
This innovation is already happening. At Savoye, we are leading the way in warehouse automation with our AI-driven robotic arms. Equipped with camera vision, this equipment can detect and decide how to pick items. Additionally, machine learning algorithms enable these robots to learn and improve over time, becoming more efficient like a human would through experience.
On the software side, our WMS solution ODATiO incorporates AI for labour management and inventory control. It uses both historical data and predictive analytics to optimise inventory management, forecasting future conditions and operations while learning from past performance.
While AI and robotics have existed for decades, the current major shift is that they are becoming more widely available and integrated into everyday warehouse operations, providing a smarter, more efficient, and adaptable approach to warehouse management and distribution centres.
LG: Are there any future plans to integrate AI in some other solutions as well?
AK: Yes, our future plans include integrating AI into other solutions as well. One of our most exciting recent developments is the introduction of the Barcode-Free Warehouse, a cutting-edge research and development project.
While a full rollout of this may take a decade, we are already making great strides. The idea is to eliminate the need for barcodes on items – a dream of any logistics manager.
For this project, the concept is to use camera vision to detect items without needing a barcode scan. When an item passes in front of the camera, a Barcode-Free Warehouse can identify it as, for example, a bottle or Item A or B, without scanning a barcode.
Once the item is placed into a tote or pallet, LiDAR technology (similar to radar) scans and confirms that the item has been placed in the correct location. The system works like the human brain, which automatically recognises shapes and colours. Just how a person can tell the difference between a bag of chips and a bottle, the cameras will do the same for items in the warehouse.
This technology involves 360° cameras that not only detect items but also confirm where they should be placed. The project is still in its pilot and R&D phase, but we are committed to driving innovation and thinking ahead by 10 years to push the boundaries of what is possible in warehouse management.
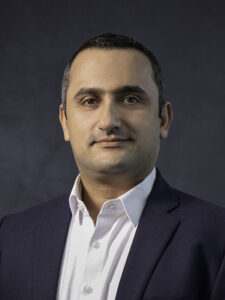
LG: With the rapid growth of e-commerce, how can technology address challenges that relate to last mile delivery?
AK: For eCommerce, the real value of a warehouse management system (WMS) comes from its ability to go beyond just managing operations within the warehouse. It is essential to consider last-mile delivery needs during warehouse planning and operations to optimise supply chain operations. As the final leg of the journey, last-mile delivery directly impacts customer satisfaction. Let me give you two key features that help tackle last-mile challenges:
Pre-cubing system: This feature allows us to choose the correct item and carton sizes for the end customer. By optimising the space inside delivery trucks, we can cut down on the number of trips required, making last-mile delivery more efficient.
Seamless integration between WMS and last-mile delivery systems: Real-time coordination is key. Instead of preparing orders and leaving them staged for hours until the last-mile team arrives, this integration ensures that orders are fulfilled, packed, and ready exactly when the last-mile delivery starts.
The last thing a logistics manager wants is a backlog of orders sitting around waiting for pickup. With the right software, WMS and last-mile systems work together to streamline the process, reducing delays and improving overall delivery efficiency.
LG: How can logistics companies create more resilient and agile systems to adapt to changing conditions? What is your advice for companies?
AK: The most important advice I would give to logistics companies seeking to build resilient and agile systems is to focus on integration rather than just mechanical solutions. Fifteen years ago, the focus was on mechanising operations, but today it is all about how well different technologies are connected. In the present age, success hinges on creating an interconnected ecosystem that seamlessly integrates technology across various supply chain operations, enhancing efficiency.
Beyond just solutions, it is essential for a company’s software to be connected with the ERP systems, last-mile delivery platforms, inventory management, and invoicing systems. The goal is to create a network of solutions that communicate effortlessly with each other.
For example, at Savoye, we developed ODATiO, which is made up of three modules – Order Management System (OMS), Warehouse Management System (WMS), and Transport Management System (TMS).
These modules can work independently or as part of an integrated whole. The key is that they are all natively connected to handle everything – from sequencing and orchestrating orders to managing the fulfilment process inside the warehouse and coordinating transportation.
By focusing on these connected, adaptable systems, logistics companies can stay agile and quickly respond to changes in the supply chain. Integration is no longer a nice-to-have; it is a must-have for companies aiming to thrive in today’s fast-evolving landscape.
LG: Sustainability is growing priority in logistics. How can technology help the industry minimise environmental impact while improving efficiency?
AK: Sustainability is becoming a crucial priority in logistics. To achieve true sustainability in the industry, it is essential to adopt a pragmatic approach that balances three pillar –people, planet, and profit. At Savoye, we understand that neglecting any one of these pillars undermines the very concept of sustainability.
Therefore, we aim to create solutions that impact all these aspects simultaneously. For example, our packing machine – Jivaro – reduces carton sizes, leading to increased efficiency by allowing more items to fit in fewer trucks, thus lowering carbon footprints.
Furthermore, our software, ODATiO, further optimises packaging by determining the appropriate carton sizes for items, thereby minimising waste and packing material. This not only decreases the size of shipped goods but also reduces transport fuel consumption.
While we envision a carbon-free future, we must also recognise that businesses need to be profitable. Therefore, as logistics companies, we should be taking small, impactful steps towards sustainability that are both practical and economically viable.